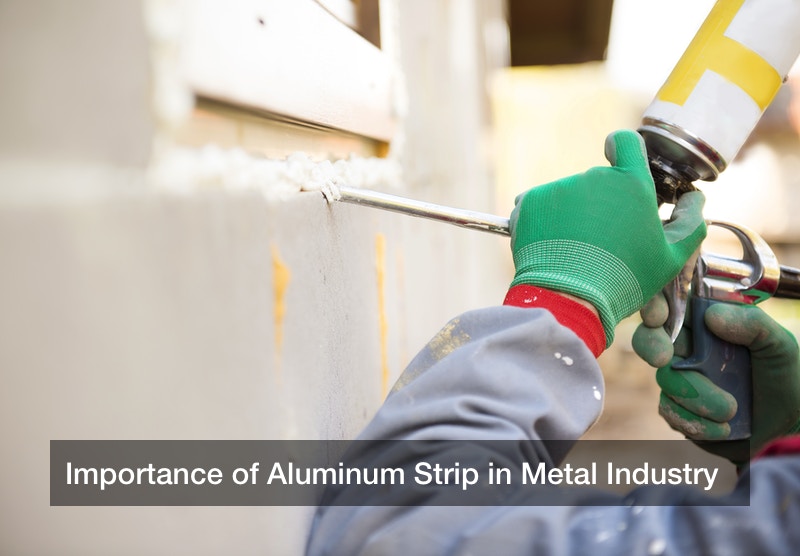

According to the U.S. Bureau of Labor Statistics, the projected growth for the metal fabrication industry is 9% from 2016 to 2026 and create more than 12,000 jobs in the sector. The most widely bought primary metals are aluminum in the shape of a bar, strip, tube, sheet or plate form, hot or cold rolling steel, and stainless steel.
Importance of Aluminum Strip in Metal Industry
Aluminum strip is an essential basic material for the growth and development of the national economy. It’s rich in aluminum content at about 99.5% purity, and the better metal properties of this series of aluminum tape include excellent thermal and electrical conductivity, corrosion resistance, highly flexibly, and plasticity. The different types of aluminum such as 6061 aluminum and 3003 aluminum have varying and unique characteristics.
The properties make aluminum strip suitable for fabrication processes such as deep drawing, extrusion, and stamping commonly used in the production of aluminum electrical products like lamps and other electronics.
Aluminum Strip: Aluminum Rich Metal Alloy
What are combined metals? These are metal fabricated with a mixture of other alloy elements and the aluminum strip is a good example of aluminum alloy made from slitted aluminum coils. The aluminum strip has a cross-sectional rectangular shape with uniform thickness. Also, it comes a range of grades such as the 1000 series, 3000 series, 5 series and 8 series with different other models including 6061 aluminum, 1050, 1060, 1070 among others.
Aluminum strip optimized fabrication processes produce highly-precise capacitor shell with high forming rate, low earring rate, and low aelotrophy. The main process used in aluminum alloy production are sub-cooling casting, metal rolling, cold rolling and two annealing processes. Such alloys are suitable compared to conventional aluminum strip made using low-quality alloy elements.
When it comes to the production of any grade of aluminum strip, whether 6061 aluminum or 3003 aluminum, the two annealing process has been significantly reduced to improve on the production efficiency, energy-efficient as well as minimum gas pollution.
Aluminum Strip Alloy Fabrication
- Melting is the first step and it has to accomplish certain requirements to ensure the product is prime for the next stage. Such requirement include complete slagging-off, uniformity, degasification and stirs full to ensure proper melt quality.
- Casting process uses rotation air blast and low condensate depression rolling casting technology to ensure quality casts. This technology helps to control casting district and cooling intensity during the degasification process, which ensures optimum performance and improves the overall quality of the metal casts.
- Cold rolling
During cold rolling, which is normally done under room temperature, the metal sheet or strip is placed in between compressing and squeezing rollers, where modification is done according to the manufacturer’s preference. Essentially, the thickness, hardness and other material properties of an aluminum strip will depend on the amount of pressure the metal is subjected to. - Annealing process uses heat treatment method to balance rolling texture, increase ductility and reduce the anisotropy of material as well as its hardness.
After the alloy has been cold rolled into foil, it’s important to use alcohol or acetone when cutting into strips. The solution helps to reduce scratch, scuffing and damaging the surface. From here, the material is ready to be used to make a range of products.